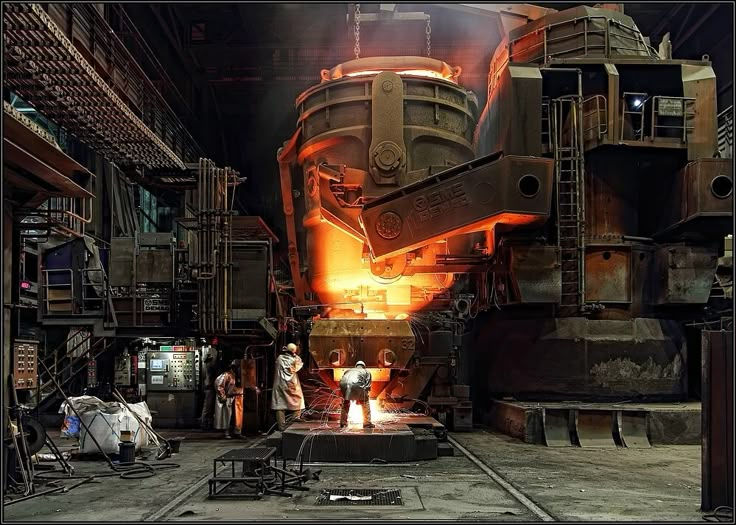
Operational
Excellence
To drive operational excellence in manufacturing organizations by enhancing efficiency, reducing waste, improving quality, and embedding a culture of continuous improvement, ensuring sustainable profitability and global competitiveness.
Key Areas of Work
1. Diagnostic Assessment of Current Operations
-
Comprehensive analysis of current manufacturing operations, including production, quality, maintenance, supply chain, and logistics.
-
Value Stream Mapping (VSM) to identify bottlenecks, inefficiencies, and areas for improvement.
-
Operational benchmarking against industry best practices and world-class standards.
2. Lean Transformation and Waste Elimination
-
Deploy Lean Manufacturing tools (5S, Kaizen, SMED, Kanban, JIT) to streamline processes.
-
Identify and eliminate the 8 types of waste (defects, overproduction, waiting, non-utilized talent, transportation, inventory, motion, extra processing).
-
Standardize work processes for stability and repeatability.
3. Six Sigma Deployment for Quality Excellence
-
Train and certify internal teams in Six Sigma (Green Belt, Black Belt programs).
-
Implement DMAIC (Define, Measure, Analyze, Improve, Control) methodologies to solve chronic problems.
-
Build data-driven decision-making capabilities to enhance process capability and customer satisfaction.
4. Production System Optimization
-
Develop customized Manufacturing Operating Systems (MOS) tailored to the client’s industry and scale.
-
Introduce visual management systems, daily management routines (Gemba walks, tiered meetings), and escalation processes.
-
Integrate operational KPIs with real-time dashboards for proactive performance monitoring.
5. Total Productive Maintenance (TPM) Programs
-
Implement Autonomous Maintenance, Planned Maintenance, and Predictive Maintenance systems.
-
Increase Overall Equipment Effectiveness (OEE) through machine reliability initiatives.
-
Build cross-functional teams for equipment ownership and downtime reduction.
6. Digitalization for Smart Operations
-
Identify and implement Industry 4.0 technologies (IoT, AI, Digital Twins) to optimize operations.
-
Deploy Manufacturing Execution Systems (MES) for production tracking and optimization.
-
Enable predictive analytics for maintenance, quality, and supply chain efficiencies.
7. Workforce Development and Culture Building
-
Develop Operational Excellence Leadership Programs.
-
Empower frontline teams with problem-solving tools and ownership mindsets.
-
Establish a culture of Continuous Improvement (CI) through regular Kaizen events and suggestion systems.​
​