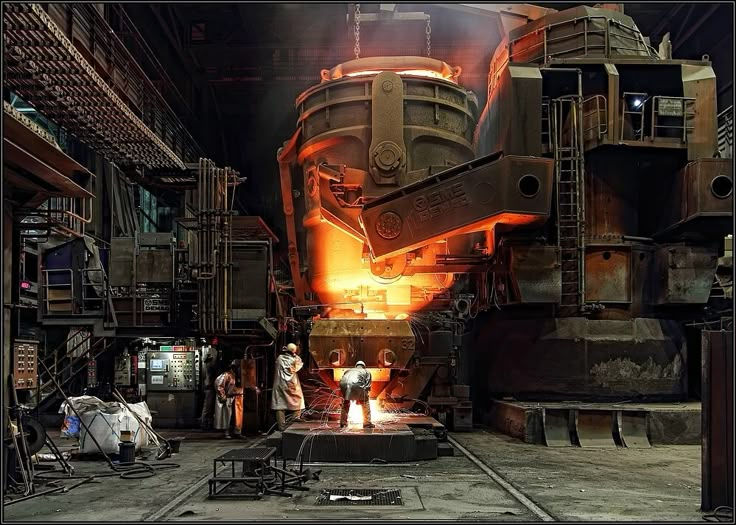
Grey & Ductile
Iron Castings
To transform the client’s Grey & Ductile Iron Foundry into a world-class, highly profitable operation by deploying best-in-class practices in process excellence, quality leadership, technology modernization, cost optimization, and organizational capability building.
Key Areas of Work
1. Strategic Diagnostic and Benchmarking
-
Conduct a comprehensive audit of current foundry operations: production, quality, maintenance, supply chain, energy usage, and workforce practices.
-
Benchmark against global best practices (top-performing foundries internationally).
-
Identify critical performance gaps (productivity, yield, cost structure, delivery, quality).
2. Foundry Process Optimization
-
Redesign and standardize key processes (molding, melting, pouring, cooling, fettling, machining) for best quality and throughput.
-
Optimize metallurgy and charge mix designs to maximize yield and minimize raw material cost.
-
Reduce scrap and rework rates through real-time quality control systems and Root Cause Analysis (RCA).
3. Quality Excellence and Zero Defect Culture
-
Deploy a robust Quality Management System (QMS) aligned with ISO 9001/IATF 16949 (if automotive).
-
Implement in-process quality control (IPQC) and Statistical Process Control (SPC).
-
Drive "Zero Defect" mindset with mistake-proofing (Poka-Yoke), First Time Right (FTR) initiatives, and final inspection improvements.
4. Energy and Cost Optimization
-
Perform detailed energy audits (furnace, compressor, sand plant, etc.).
-
Optimize energy consumption per ton of casting produced (target kWh/ton improvements).
Streamline supply chain and procurement strategies to reduce working capital and raw material costs.
5. Lean Manufacturing and Productivity Improvement
-
Introduce Lean methodologies (5S, SMED, Kanban, Value Stream Mapping) across the foundry.
-
Improve equipment uptime using Total Productive Maintenance (TPM).
-
Introduce real-time monitoring systems for productivity, OEE (Overall Equipment Effectiveness), and process stability.
6. Digitalization and Smart Foundry Initiatives
-
Guide adoption of Industry 4.0 technologies like IoT sensors, digital quality tracking, furnace automation, sand control systems, and predictive maintenance.
-
Deploy data dashboards for monitoring scrap rates, cycle times, downtime, and energy consumption.
7. Workforce Development and Cultural Transformation
-
Build Foundry Excellence Teams (cross-functional task forces).
-
Conduct continuous training in best practices, quality control, problem-solving (e.g., 8D, A3 thinking), and operational leadership.
-
Establish a performance-driven, high-engagement culture through skill matrices, rewards systems, and accountability frameworks.
8. Business Growth and Customer Diversification
-
Support in improving delivery performance (OTIF - On-Time In-Full) to become a preferred supplier.
-
Identify opportunities to diversify customer base (e.g., move into higher-margin sectors like non automotive, hydraulics, energy parts).
-
Develop business strategies for scaling profitably and sustainably.